- Energy efficiency
Energy efficiency is key to increasing the competitiveness of businesses amid rising energy costs. The adoption of robotics contributes to reducing energy consumption in manufacturing in many ways. Significant energy savings can be achieved by reducing heat compared to conventional assembly lines. At the same time, robots work at high speeds, which increases productivity, making manufacturing more time- and energy-efficient.
Today’s robots are designed to consume less energy, reducing operating costs. In order to achieve sustainability goals in production, the company uses industrial robots equipped with energy-saving technologies: for example, the robot control converts kinetic energy into electrical energy and feeds it back into the grid. The technology significantly reduces the energy required to run the robot. Another feature is the Smart Power Saving Mode, which controls the robot’s energy supply on demand throughout the working day. Since even today industrial facilities need to monitor their energy consumption, this connected power sensor is likely to become the industry standard for robotic solutions. - Bots get easier to use
Robot programming has become easier and more accessible to non-experts. Providers of software-driven automation platforms empower companies to let users manage industrial robots without programming experience. OEMs are working with low-code or even no-code technology partners to make programming robots accessible to users of all skill levels.
Easy-to-use software combined with an intuitive user experience replaces extensive robot programming and opens up new robotic automation opportunities: software startups are entering this market with specialized solutions that meet the needs of SMEs. For example, traditionally heavy industrial robots could be equipped with sensors and new software that allow collaborative setup operations. This allows workers to easily adjust heavy machinery for different tasks. As a result, companies get the best of both worlds: powerful and precise industrial robot hardware and state-of-the-art cobot software.
An easy-to-use programming interface that allows customers to set up robots themselves is also driving the nascent field of low-cost robotics. Many new customers responded to the 2020 pandemic by experimenting with robotic solutions. Robot suppliers acknowledge this need: ease of setup and installation, for example, with pre-configured software to handle grippers, sensors or controllers, enabling low-cost robot deployment. Such robots are usually sold through online stores, and program routines for various applications can be downloaded from the application store. - Artificial intelligence (AI) and digital automation
Driven by advances in digital technology, robotics suppliers and system integrators are delivering new applications and improving the speed and quality of existing ones. Connected robots are transforming manufacturing. Robots will increasingly operate as part of a connected digital ecosystem: cloud computing, big data analytics or 5G mobile networks provide the technical basis for optimized performance. The 5G standard will fully digitize production and make cables on the shop floor obsolete.
Artificial intelligence (AI) holds great potential in robotics, bringing a range of benefits to manufacturing. The main purpose of using AI in robotics is to better manage variability and unpredictability in the external environment in real-time or offline. This enables AI-enabled machine learning to play an increasing role in software products, benefiting the systems that run
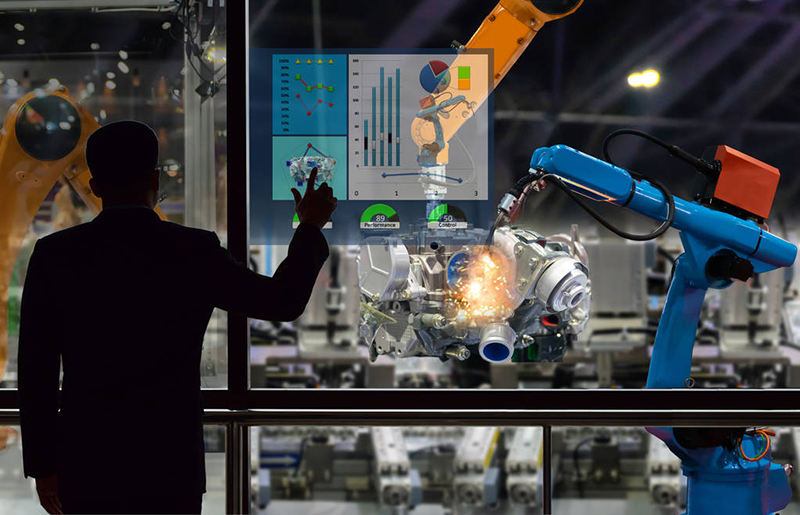
How many axes does an industrial robot have?
The axis of the so-called